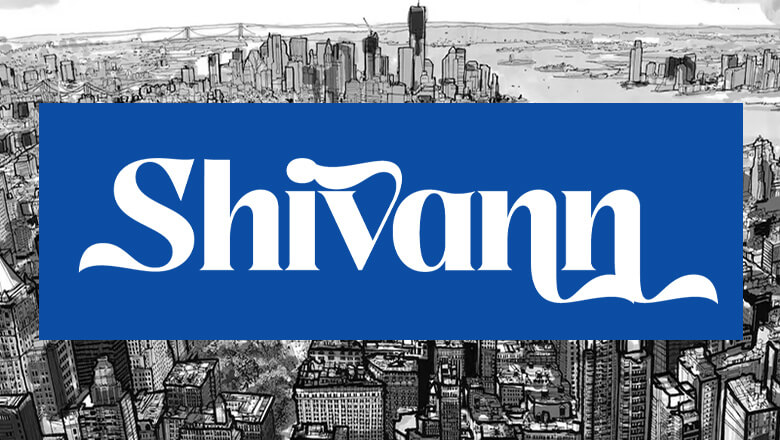
views
Even as terracotta is an evolved art form in the State, very few artists have realised the possibility of ceramics. The origin of ceramics as studio pottery may be a recent development but it has caught up silently as some art institutes are offering pottery as an elective course in the department of sculpture.In Bhubaneswar the opportunities may be next to nil, but there have been attempts by artists to gradually promote an appreciation for ceramics or studio pottery. Though peripheral, a handful of artists such as Krupasindhu Barik, Swapam Kumar Jana, Jayant Kumar Das - who can be called ‘educated potters’ - have experimented with ceramics to some extent.The three artists participated in a six-day regional workshop on crystalline glaze, a technique of ceramic pottery, at the regional Lalit Kala Akademi that concluded on Monday. The aim was to popularise ceramic pottery and the specific medium of glazing which is much in demand these days.The struggle for sustenance that the local potters undergo is a known story to all the three. Ceramics like terracotta is made locally and distributed locally, without having any kind of organised market or infrastructure to promote it. “Through workshops like these, we want to tutor the potters and artists alike in high temperature, glazed ceramics, which allows them not only to make pottery that is much more resilient but also to explore with colours and design. This will give them an opportunity to incorporate changes to accommodate this new technology of crystalline glaze. In fact, ceramic pottery with crystalline glaze can open up an entirely new facet of pottery that has higher market value,” Krupa says.Explaining this new technique, he says the glaze, which is a form of glass, is made from various raw ingredients including zinc that are all mixed together with water and applied to the pot before it is fired. “The glaze is a mixture and the crystals form in the course of the firing. The glaze has to be extremely fluid when it is above 1000 degrees C to enable the crystals to grow, and surplus glaze runs off the pot. The kiln has to be fired in a special way to help the glaze grow good crystals. Usually the kiln is fired quite rapidly to the maximum temperature, then it is cooled by about 200 degrees C, and the kiln is held at that temperature for several hours. It is in this holding period that the crystals grow. By making little dips and spikes in the temperature that the kiln is held at, it is possible to form growth rings in the crystals,” Krupa adds. The three feel although, the resources in the medium are plentily available here, they have not been exploited as factors like firing and glazing are expensive propositions for the artists.Says Swapan: “Even though industrial ceramics flourish in our State as the region is rich in minerals, getting clay, the process of firing and then glazing punctuates it with limitations.” Jayant adds, if adopted on a large-scale, ceramic pottery with crystalline glaze can bring about a massive change in the livelihood of potters and local artists.While Krupa did his masters in ceramic form from Benaras Hindu University, Swapan pursued the study from Government College of Art and Craft, Kolkata and is at present, a professor in the subject there. Likewise, Jayant is a professor in ceramics in the B K College of Art and Craft.Explaining that the workshop was a first-of-its-kind in the State, the three are hopeful of organising more such events with the help of the Akademi and other bodies to popularise the art form.The products that were created during the workshop were a mix of the traditional and the contemporary and in colours ranging from soft, sensual tones in peach and pink to fiery burgundy and alluring blues. They were put on exhibition at the Akademi on Monday evening.
Comments
0 comment