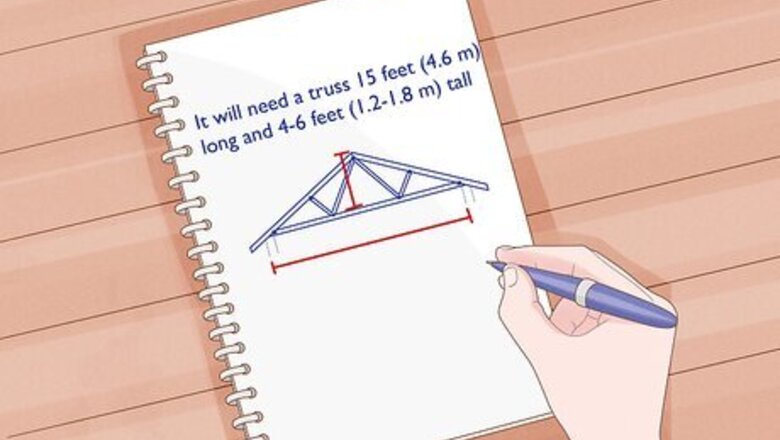
views
Selecting the Right Type of Truss
Measure your structure to determine how big your truss needs to be. Trusses can be built in many different shapes and sizes to accommodate the dimensions of various structures. Before you can begin plotting the exact specifications of your truss, find the overall length and height of the structure being reinforced. A truss for a gable roof on one side of your home, for example, might need to be 15 feet (4.6 m) long and 4–6 feet (1.2–1.8 m) tall. The dimensions of your structure will determine the angles formed by the truss’s top and bottom beams, or “chords.” On a relatively shallow roof, for instance, the upper and lower chords may meet at a 30-degree angle on each side. In some cases, building codes may dictate the size requirements of a truss for a certain type of structure. Be sure to consult your local building codes before you begin drawing up plans for your truss.
Use a simple king post truss to reinforce small, lightweight structures. A king post truss design features a single vertical joist that runs through the center of the triangular frame. This style is useful for framing structures that don’t require quite as much support as structures that bear more weight. A king post truss may be all you need if you're looking to add some extra stability to a garden shed or gable roof.
Build a Fink truss to bolster a floor, roof, or deck. In a Fink truss, the internal joists are arranged in a “W” shape, ensuring even weight distribution from one end to the other. Fink trusses were originally invented for the purpose of beefing up bridges, but many contractors now use them to increase the strength of interior structures. When fashioning a Fink truss, the middle of the "W" will be at the center line of the triangle. Similarly, the points formed by the internal joists will connect at the midpoints on either side of the center line. Due to the symmetrical simplicity of their design, Fink-style trusses can also make an attractive alternative to plainer styles for ornamental structures like gazebos and covered outdoor shelters.
Construct a Howe truss to provide unshakable support from below. Howe trusses closely resemble the King Post and Fink styles, only with additional angled beams arranged around the central joist at regular intervals. They are often built onto the underside of the structure they're intended for. The internal angles in a Howe truss are repeated at regular intervals. Both sides of a standard Howe truss, for example, might consist of joists forming opposing 90 and 60-degree angles. Because of their complex configuration, Howe trusses tend to be difficult to plan and assemble, and are most often reserved very large load-bearing structures. A Howe-style design will offer maximum reinforcement for multi-level structures, as well as those built from especially heavy materials.
Designing Your Truss
Size the bottom chord 0.25 inches (0.64 cm) longer than the floor. Start by noting the exact length of the structure’s floor. Then, add 0.25 inches (0.64 cm). This will account for possible inconsistencies and ensure that the truss is a proper fit. If possible, use a tape measure to double-check the floor’s length rather than simply relying on the recorded measurements listed in the building plan.
Incorporate overhanging top chords to add extra visual flair. On some roof trusses, the 2 top chords extend down over the edges of the bottom chord, creating a built-in overhang. If you think you’d prefer an overhang-style truss, adjust the measurements for your top chords accordingly. Your top chords can protrude beyond the bottom chord anywhere from 1–3 feet (0.30–0.91 m). Overhanging chords are more of a stylistic feature than a practical one, and shouldn’t affect the overall stability of the truss.
Cut plywood gusset plates to fasten together lightweight trusses. Gusset plates are used to secure the connections between the individual truss components. Fashion your own set of plywood gusset plates by cutting thick sheets of plywood to fit over each site where one joist meets another. This will include all 3 corners of the frame, as well as the top and bottom of each beam crisscrossing the center of the truss. Use a circular saw or skill saw to cut your plywood to the right size and shape. Making your own plywood gusset plates will help you keep the overhead for your project low.
Use steel gusset plates to secure trusses for weight-bearing structures. Depending on the scale of your project and the specific building codes in your area, you may have the choice to use galvanized steel gusset plates. While these won't be necessary for most projects, they can come in handy for holding together trusses designed for bridges, cathedral-style roofs, or other especially large structures. You can order steel gusset plates from companies that specialize in construction timber or steel-working supplies. Solid steel gusset plates cost quite a bit more than plywood ones, so make sure they fit into the budget you've set for your project.
Create a detailed sketch of your truss design. Once you have all of your measurements worked out, commit your plans to a sheet of graphing paper. Draw each of the major lines and angles to scale, being sure to note their exact specifications out to one side. Alternatively, you can use an architectural design software to generate a diagram based on the specific measurements you assign. If you’re drafting up your plans by hand, use a ruler to make sure that your lines are straight and the internal angles of the truss are accurately represented. You can find many helpful digital design programs for free or cheap online.
Submit your building plans to your local licensing authority. Most cities have agencies responsible for overseeing building codes and regulations. After completing the design for your wood truss, you’ll need to submit a copy to the licensing department for your region in order to have it approved for construction. If you’re not sure who the licensing authority for your area is, run a quick search for “construction licensing” plus the name of your city, state, or territory. The criteria used by your licensing department may differ depending on factors like zoning laws, geographical features, and weather patterns. For example, if you live in an area with heavy snowfall, your city will likely have strict requirements about the bearing strength of your new structure. Building codes may not apply if you’re just constructing a truss for simple structures like a small tool shed.
Putting the Truss Together
Measure and mark your timber with a pencil. Before you begin sawing your raw materials, lay out your lumber on a flat surface and trace a line where you plan on making each cut. Precise measurements are critical if you want your truss to be sturdy and fit together properly. Refer back to the plans you drew up to keep track of how long each piece of lumber needs to be. Use a triangle square to verify the angles at the edges of the top and bottom chords. Trusses for common structures like houses, carports, and gazebos are most often constructed using 2 in (5.1 cm) x 4 in (10 cm) wooden boards.
Cut your truss pieces to size using a jigsaw. A jigsaw will allow you to make short crosscuts through thick pieces of wood with maximum efficiency. Set your lumber on a shop table or between 2 sawhorses and guide the saw smoothly across the measurement lines you drew earlier to achieve clean, precise cuts. To prevent the pieces from shifting, consider using a table clamp to hold them fast to your work surface. Always wear gloves and safety glasses to protect yourself from injury while operating a power saw.
Assemble your truss in the desired shape. After cutting your lumber, gather up the individual pieces and begin fitting them together. Remember, you’ll need 2 top chords, 1 bottom chord, and at least 1 central joist for support. Study your plans closely to make sure you're piecing the internal joists together in the correct configuration for the style you've chosen. Keep in mind that the angles formed by the internal joists will remain the same despite differences in the frame's height or width. This is a good opportunity to visually confirm that each component has been cut to the correct size. If you encounter any mistakes, you may need to start over with a fresh piece of lumber.
Use construction adhesive to hold the truss components together. Apply a generous amount of adhesive to the face of each piece where it will intersect with the next using a putty knife. Then, carefully return the piece to its place in the assembly. Press the 2 connecting pieces together for 30-40 seconds to ensure that the adhesive sticks firmly. For ease of application, look for glues that come in tubes similar to caulk guns. Take your time to make sure everything is where it needs to be. With most adhesives, you’ll have a window of 10-15 minutes before the adhesive begins to set. This will allow you to reposition your components as needed.
Attach gusset plates at each connection site to fasten the finished truss. Apply a thin layer of construction adhesive to the backside of a plate. Then, flip it over and press it firmly into place over a joint between two truss beams. Insert construction screws every 2–3 inches (5.1–7.6 cm) through the holes in the face of the plate and use an electric drill drive the screws deep into the wood. Repeat this process at each remaining joint. If you're working with plywood gusset plates, you can drill your screws directly through the plates themselves. Give the adhesive 1-2 minutes to bond before installing the screws. That way, the friction of the drill won’t cause the plates to slip out of place. Allow the adhesive to set overnight. The following day, your truss will be ready to add on to the structure it’s intended to support.
Comments
0 comment